Comprehensive Guide: What is Porosity in Welding and Exactly How to avoid It
Comprehensive Guide: What is Porosity in Welding and Exactly How to avoid It
Blog Article
Porosity in Welding: Identifying Common Issues and Implementing Ideal Practices for Avoidance
Porosity in welding is a prevalent problem that typically goes undetected up until it causes considerable issues with the honesty of welds. In this conversation, we will discover the crucial aspects contributing to porosity formation, examine its destructive impacts on weld efficiency, and go over the ideal techniques that can be embraced to minimize porosity incident in welding processes.
Usual Reasons of Porosity
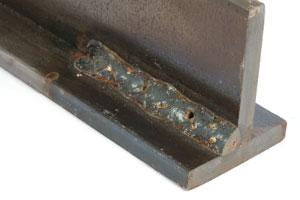
Utilizing unclean or wet filler products can introduce impurities right into the weld, contributing to porosity concerns. To reduce these common causes of porosity, thorough cleansing of base metals, correct securing gas choice, and adherence to optimal welding specifications are necessary techniques in achieving top quality, porosity-free welds.
Effect of Porosity on Weld Quality

The existence of porosity in welding can considerably jeopardize the structural stability and mechanical homes of welded joints. Porosity produces spaces within the weld metal, deteriorating its general toughness and load-bearing capability.
One of the main effects of porosity is a decrease in the weld's ductility and strength. Welds with high porosity levels have a tendency to display lower effect stamina and lowered ability to warp plastically before fracturing. This can be particularly worrying in applications where the welded parts undergo vibrant or cyclic loading problems. Additionally, porosity can hinder the weld's ability to properly transmit pressures, bring about premature weld failing and prospective security dangers in critical frameworks.
Ideal Practices for Porosity Avoidance
To enhance the architectural stability and quality of bonded joints, what certain steps can be executed to minimize the event of porosity during the welding process? Making use of the correct welding method for the certain material being bonded, such as readjusting browse around this web-site the welding angle and weapon placement, can even more avoid porosity. Routine evaluation of welds and immediate removal of any concerns recognized throughout the welding process are important techniques to prevent porosity and create high-grade welds.
Significance of Proper Welding Strategies
Implementing proper welding techniques is paramount in guaranteeing the structural integrity and high quality of welded joints, building upon the foundation of effective porosity avoidance procedures. Excessive warmth can lead to raised porosity due to the entrapment of gases in the weld swimming pool. In addition, making use of the proper welding specifications, such as website here voltage, present, and take a trip rate, is critical for accomplishing sound welds with very little porosity.
In addition, the option of welding process, whether it be MIG, TIG, or stick welding, must align with the details needs of the project to make certain ideal outcomes. Correct cleansing and preparation of the base steel, as well as choosing the right filler material, are also essential elements of proficient welding methods. By sticking to these finest techniques, right here welders can reduce the danger of porosity development and produce premium, structurally audio welds.

Examining and Quality Assurance Steps
Evaluating treatments are important to identify and avoid porosity in welding, making certain the stamina and toughness of the last product. Non-destructive testing techniques such as ultrasonic testing, radiographic testing, and aesthetic examination are generally used to determine prospective problems like porosity.
Post-weld evaluations, on the various other hand, assess the final weld for any kind of problems, consisting of porosity, and validate that it satisfies defined criteria. Executing a thorough top quality control plan that includes detailed testing procedures and assessments is paramount to decreasing porosity problems and making certain the overall high quality of bonded joints.
Verdict
To conclude, porosity in welding can be a typical problem that influences the quality of welds. By determining the typical reasons of porosity and executing ideal techniques for prevention, such as appropriate welding strategies and screening measures, welders can guarantee top quality and trusted welds. It is important to prioritize avoidance methods to reduce the incident of porosity and preserve the stability of bonded frameworks.
Report this page